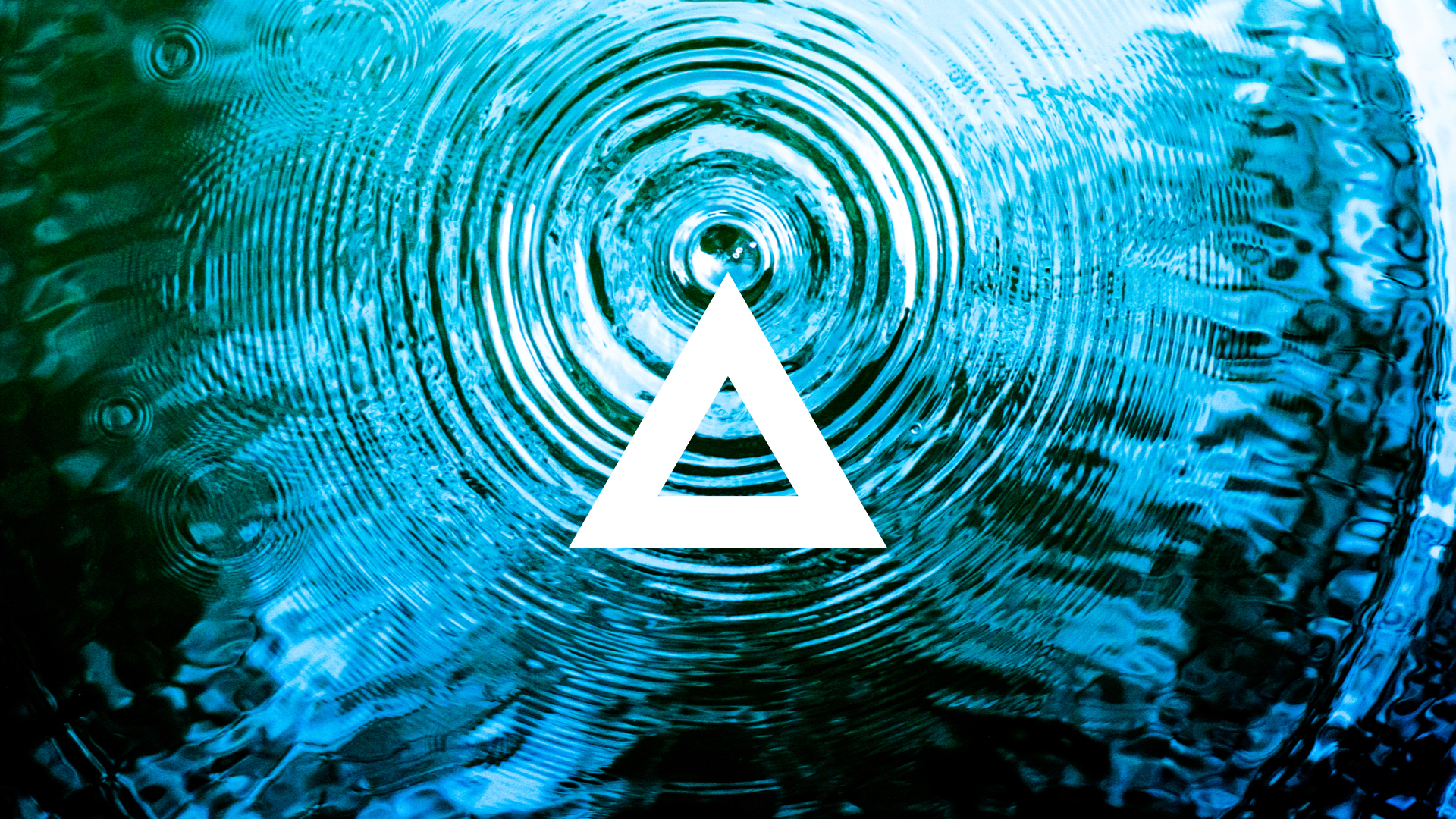
Focus areas
Water
Water
60% of Coats total water consumption is used in dyeing, one of the most important parts of the thread manufacturing process. Coats is investing in new machines with low liquor ratio. It is also exploring innovative developments in digital printing technology and the waterless dyeing opportunity that offers.
Leader's Voice
“Water is a precious resource and existential to our business. Without it we cannot make the threads our customers want. We are fortunate that in many parts of the world where we operate water is plentiful today, but in others it is not. And we know that changes in our climate may impact the availability of water that we, and the communities around us, need. Furthermore, water is a cost and so it is in our commercial interests to use this resource as sparingly as possible.
We will invest in new technology and ways to improve the efficiency of our processes, as well as implementing robust programs of management and maintenance to make sure we are not wasteful. Our businesses are targeted to use less, and this is an important priority for Coats as we strive to make more thread, using less water.”
Michael Schofer Chief Supply Chain Officer