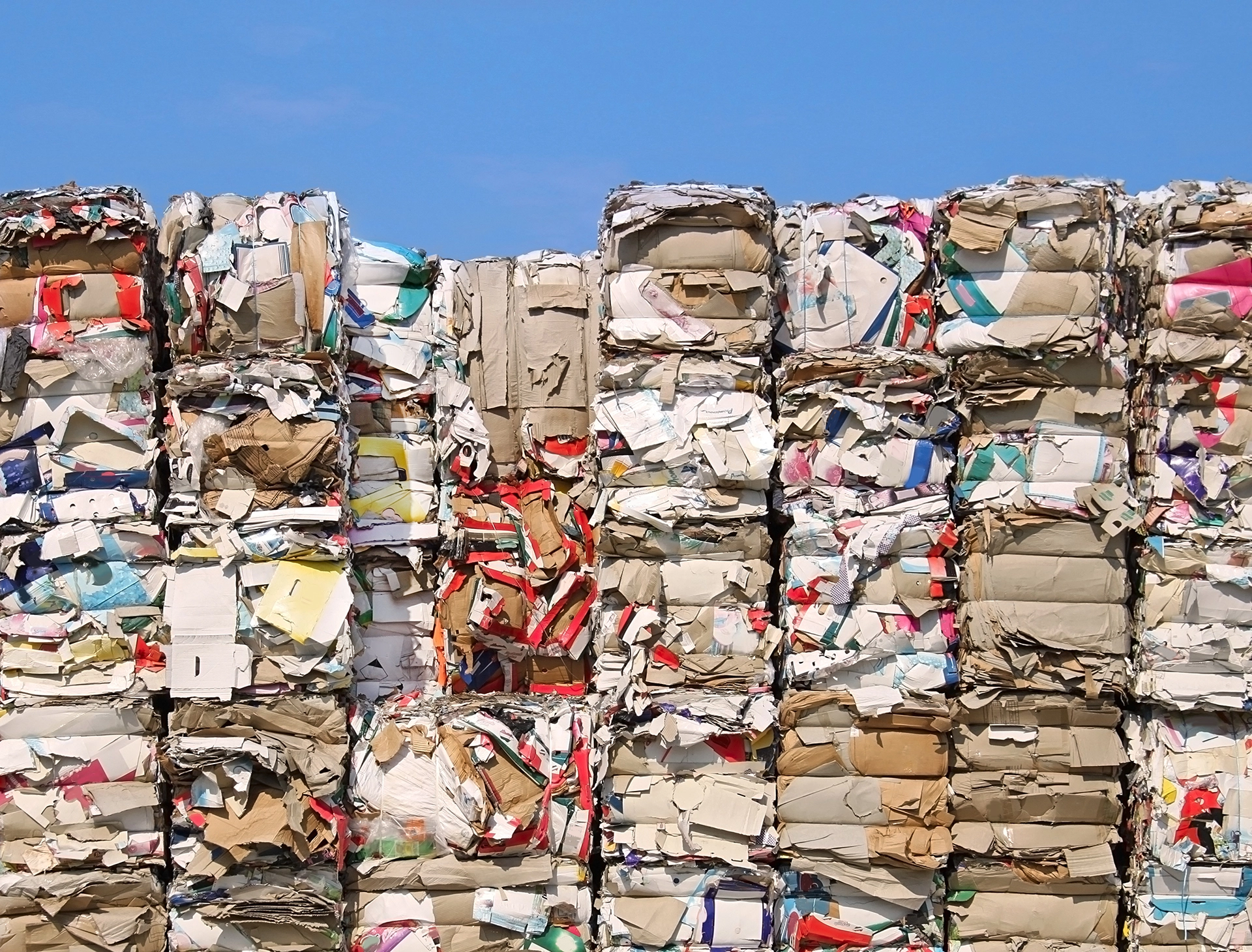
Celebrated on 18th March, 2024, Global Recycling Day serves as a reminder to strive towards the promotion and implementation of recycling initiatives.
We continually seek opportunities to minimise waste through our effective waste management strategy and sustainability initiatives. Our commitment to Sustainability and overall waste reduction is embedded in the Coats culture.
Our overall waste reduction strategy focuses on reducing landfill waste to zero, and lowering waste generation through process and product redesign, followed by the adoption of reuse and recycling programmes. In addition, Coats is committed to enhancing circularity by transitioning our production processes, material flows, and products from a linear (take, make, discard) to a circular (reduce, reuse, recycle) model.
We implemented initiatives across our various facilities to improve our awareness of waste streams, improve waste segregation, and identify more sustainable waste destinations. These measures have helped us to significantly reduce the amount of waste that ends up in landfills.
In 2023, we reduced by 37% the waste that we send to landfill, and 59% of our waste was either recycled or reused. By 2026 our goal is to have zero waste ending up in landfill destinations.
We continue to expand our recycled product range and vigorously promote sales growth in this category. In support of recycled product expansion, Coats is committed to delivering a 60% transition to sustainable raw materials by 2026; a core sustainability goal.
Circularity
In 2023, Coats continued to promote circularity within our waste management program. We have worked collaboratively with many of our supply chain partners to not only reduce waste in packaging materials, but also to adopt circular reuse and recycling methodologies on the materials which must remain in the supply chain. In 2023, we were re-supplied with a significant 2,591 tonnes of circular materials which would otherwise have been considered waste.
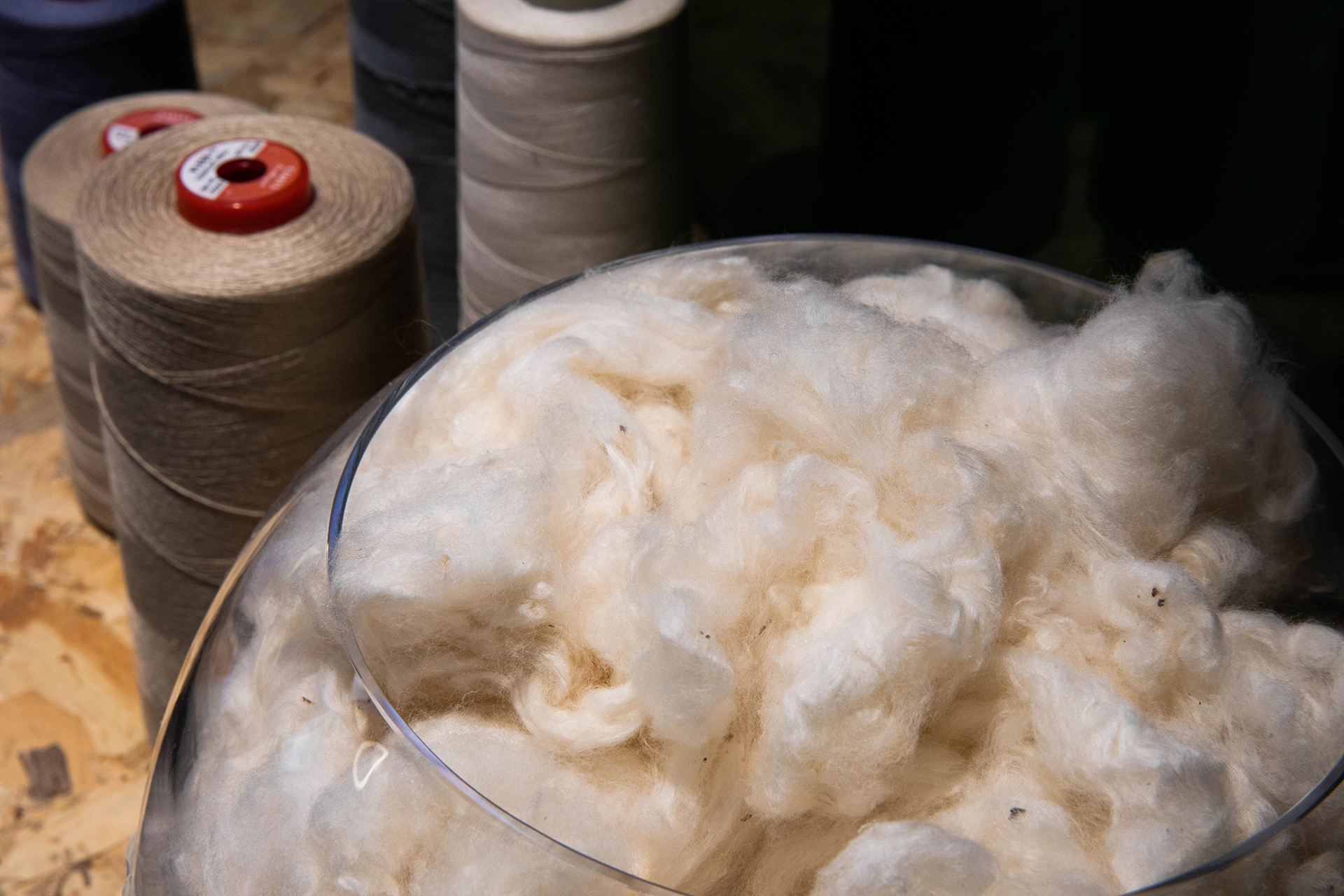
Circularity Case Study
Our team members across the Commercial, Manufacturing, Procurement and Warehouse verticals worked together with both the customers and suppliers, enabling packaging requirements to be reviewed and enhanced sustainably, while at the same time entirely meeting the required quality levels.
A significant portion of the plastic cone supports, which we use for winding finished goods thread products, is sourced from circular plastic feedstocks. These feedstocks are derived from recycled and remoulded plastic, forming a closed-loop system originating from the plastic ‘dyeing centres’ utilised in our dyeing process. Our manufacturing facility in Ho Chi Minh City, Vietnam, circular recycled in excess of 216 tonnes of plastic in this way in 2023, with our Romania factory circular recycling in excess of 60 tonnes in the same period.
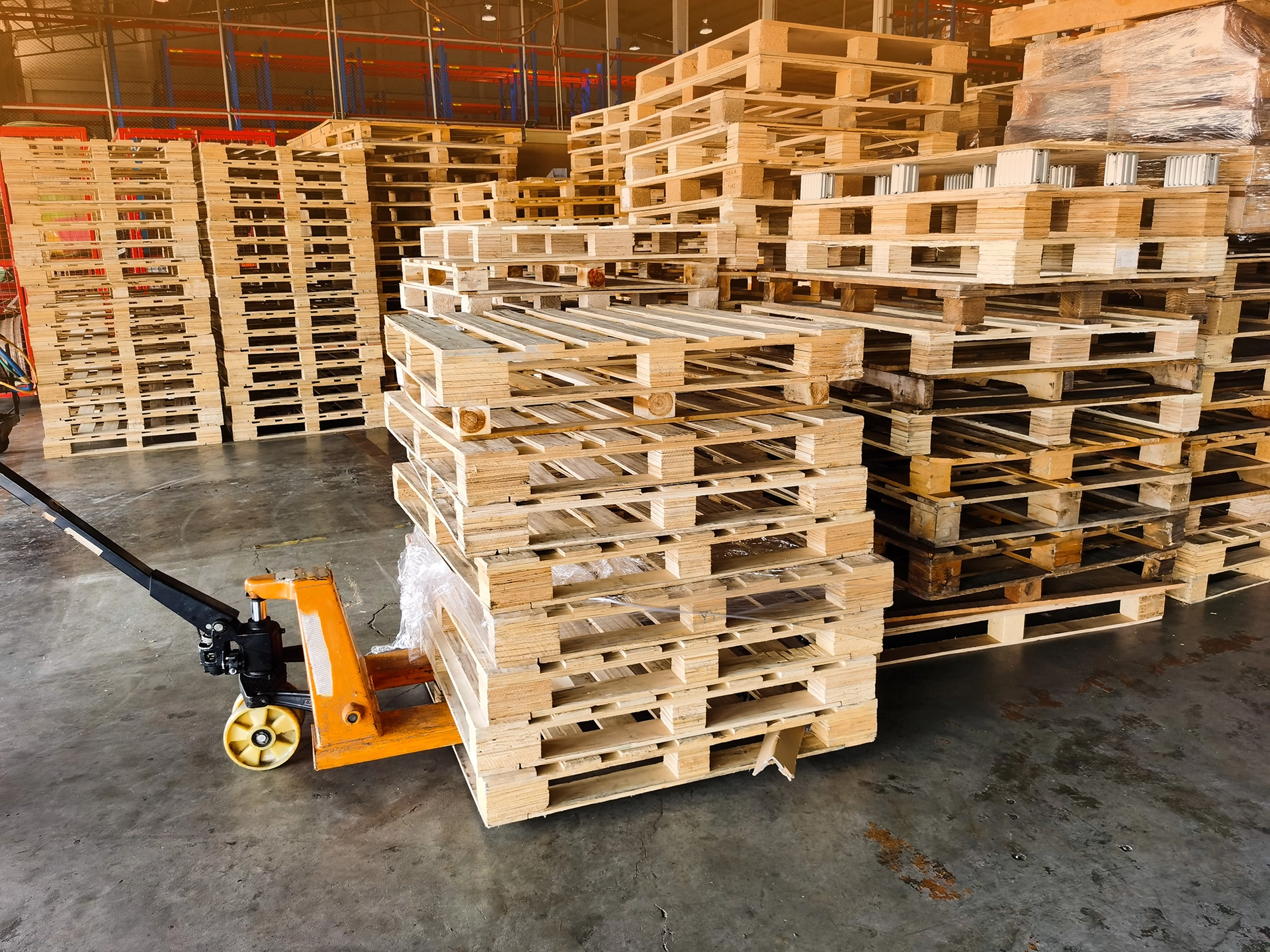
Coats EcoCycle Case Study
Coats EcoCycle is a pioneering water-dissolvable thread concept which helps facilitate end-of-life recycling when washed at the temperature of 95°C. Whilst the thread sustains its durability, quality and strength during the life span of the garment when exposed to a thermal washing process at temperatures higher than 95°C it lets the seam dissolve so that non-textile and textile components could be effortlessly separated for recycling. This product displays the potential to be genuinely transformative in driving a circular textile economy. We are seeking to bring together the key industry participants - brands, collectors, and recyclers - to scale this solution.
Sustainable Materials
Footwear structural components are shipped to the customer in sheet form. Customers cut out parts which undergo further processing, creating up to 20% waste, which is subsequently returned to Coats to remelt and recycle. The footwear team is extremely proud to offer a range of 100% recycled polyester structural solutions whilst still maintaining the key performance characteristics that we pride ourselves on.
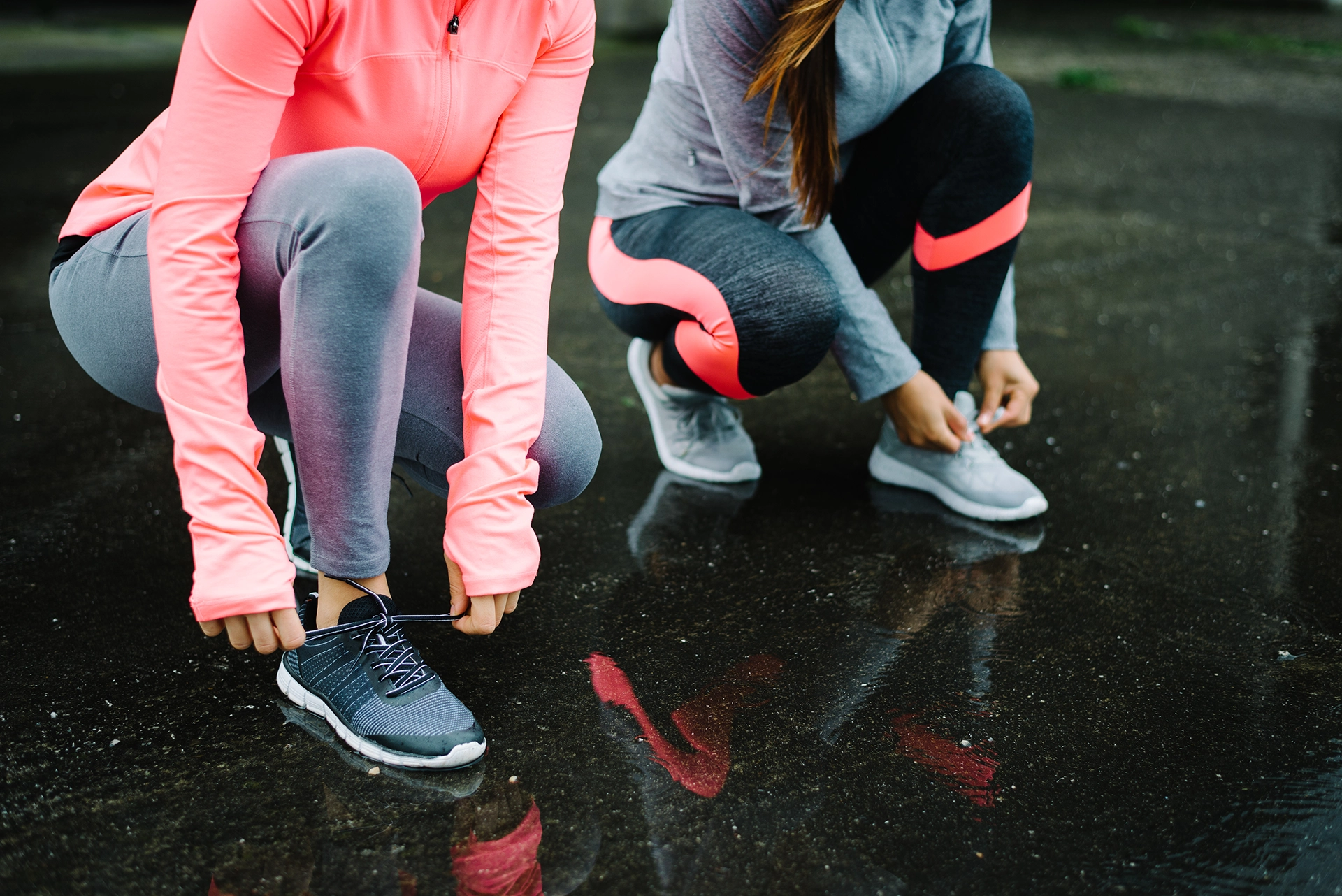
Of the filament and fibre raw materials that we consume, 93% are derived from oil-based plastics. Embedded emissions in our raw materials make up for the majority of our Scope 3 emissions, largely through the use of virgin oil-based materials. In support of the Science Based Targets Initiative, Coats is committed to eliminating all virgin oil-based materials by replacing with recycled plastics, or alternative materials sourced from cellulosics.
Important Timelines
In the year 2019, we adopted the European Union’s Waste Framework Directive as our basis for waste management. The resulting waste catalogue contains 36 different waste categories that encompass all material items present in a Coats unit. This helped with increased transparency and understanding of waste generation streams across our business, plus identification of opportunities for reduction, and, where possible, prevention.
In 2023, of the total waste generated, 59% was recycled or reused, with 9.6% disposed of in landfills (down from 13% in 2022). Worldwide, 48% of our units have achieved zero waste to landfills throughout the year, with 100% targeted by 2026.
In the same year, further focus was given to the selection and optimised use of chemistry for physical/chemical effluent treatment systems. This has resulted in higher efficacy in coagulation and flocculation and helped reduce sludge generation. Substantial progress was made in the weight reduction of sludge through the optimisation of filter-press operation and enhanced sludge drying, delivering more effective water extraction.
In 2024, we are focused on the waste work stream and upstream supplier collaboration. We plan to introduce circular material flows to establish closed-loop recycling systems. Another example of this process is our collaboration with suppliers of cardboard packaging materials. We return packaging materials to the suppliers to repulp and manufacture back into the same packaging material which is used to protect the incoming raw materials supplied to Coats. Similarly, for plastic chemical drums supplied by manufacturers, we are implementing a circular material flow - eliminating the need to classify them as waste.
Our target for 2026 is to deliver zero waste to landfills. This will be achieved by higher granularity analysis of waste streams which today continue to be diverted to landfills, with improved waste segregation and identification of opportunities for reuse, recycling, and circularity.
As we celebrate Global Recycling Day, we are committed to advancing waste reduction and recycling initiatives, while identifying and embracing new circular opportunities.